はじめに:温度・圧力制御の重要性
化学プラントにおいて、温度と圧力の安定制御は、反応速度や生成物の選択率、安全性など、プロセス全体に大きく影響を与えます。たとえば反応器の温度が高すぎれば副反応や暴走反応のリスクが高まり、逆に低すぎれば生産性が落ちる。圧力容器では、容器内部や配管の圧力が設計範囲を超えると装置破損やリークなど重大事故を引き起こしかねません。そのため、多くの現場ではPID制御(比例・積分・微分制御)を用いた温度・圧力コントロールが基本的かつ不可欠な仕組みとして運用されています。
基礎:PID制御とは
PID制御の原理
PID制御は、**偏差(目標値と現在値の差)**を元に操作量を決定する古典的な制御手法です。数式的には以下の通りです。
PID制御の基本式:
$$ u(t) = K_p \, e(t) \;+\; K_i \int_0^t e(\tau)\,d\tau \;+\; K_d \frac{d\,e(t)}{dt} $$
変数の定義:
\( e(t) \): 偏差(目標値 – 現在値)
\( K_p \): 比例ゲイン
\( K_i \): 積分ゲイン
\( K_d \): 微分ゲイン
単純な構造ながら汎用性が高く安定性も良いため、温度制御や圧力制御など様々なプロセス変数の調整に適しています。
温度・圧力制御への適用
- 温度制御:センサー(サーミスタ、RTDなど)が測定する温度と目標温度の偏差をもとに、加熱器や冷却水バルブをPID操作。
- 圧力制御:圧力計で測定した値をPID制御器へ送り、コンプレッサーの回転数や放出バルブを調整するなどして、目標圧力を保つ。
これらの制御が確立されることで、プロセスの生産性・品質安定・安全性が大きく向上します。
実務:温度・圧力制御におけるPIDの活用
反応器の温度管理
化学反応は温度に非常に敏感で、反応速度はArrhenius式に従い指数関数的に変化します。温度がわずかに上昇するだけで副反応が増えたり、暴走反応リスクが高まることがあるため、発熱反応では冷却ジャケットやクーラーをPID制御し、適切な除熱を行います。逆に吸熱反応では加熱不足で歩留まりが低下しないよう、加熱源(スチーム、ヒーターなど)をPID操作するケースが多いです。
- ジャケット温度ループ:ジャケット内の熱媒体流量を制御し、反応器内部温度を安定化。
- 外部循環ループ:反応液を熱交換器に通してから再び反応器へ戻す。流量や媒体温度をPIDで管理。
反応速度論と熱収支を踏まえたうえでPID制御のゲインを適切に設定すれば、暴走防止や高収率運転が実務的に安定して達成できます。

圧力容器やパイプラインの圧力制御
圧力を一定範囲に保つことは、化学プラントの安全運転だけでなく、下流工程の負荷安定や製品品質にも直結します。たとえば、ガスを一定圧力で供給する際には、コンプレッサーや制御弁をPID操作して目標圧力に近づけます。もし偏差が大きくなれば弁を開き圧力を逃がす、あるいはコンプレッサー出力を上げるなどの自動補正が行われます。
- コンプレッサー回転数制御:目標圧力に対して回転数を上げ下げすることで圧力を保つ。
- 圧力制御弁(PCV)制御:安全弁とは別に、PIDループで流量を調整する弁を設け、圧力が高まれば放出して安定化。
圧力の安定化は配管や装置の疲労破壊を防ぎ、設備寿命の延長にも寄与します。
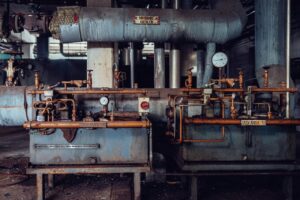
最新技術:高度制御やAIの導入
自動チューニングとMPC
PID制御はシンプルですが、最適なゲインの設定(P, I, D)の難しさが常に指摘されています。近年は以下の技術が普及しつつあります。
- 自動チューニング:ステップ応答試験をAIが解析し、ゲインを自動算出 → オペレーターの試行錯誤を削減。
- モデル予測制御(MPC):温度や圧力の制御だけでなく、他の操作変数(流量、レベルなど)を含め多変数を同時に最適化。大型プラントや相互干渉が強いプロセスではMPCがPIDを補完する。
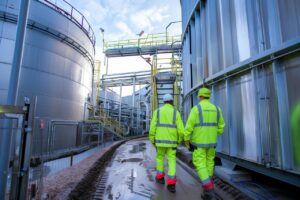
AI活用による異常検知と予測
大量の運転データをAIが学習し、プロセスの通常挙動を把握 → 偏差が大きい場合やセンサー値のパターンに異常があれば即時アラート、といった異常検知システムが登場しています。さらに、先を予測して制御入力を先回り調整する試みも研究されており、急激な負荷変動や原料切り替え時のトラブルを最小限に抑えられます。
- リアルタイム予測モデル:温度・圧力がこのままだと数分後に目標から外れる → PID操作量を補正しておく
- デジタルツイン:反応器や配管の仮想モデルをオンラインで回し、操作の結果を先にシミュレート
これにより、PID制御が本来苦手とする大きな外乱や突然の原料組成変化にも柔軟に対応できるようになりつつあります。
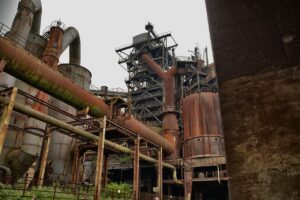
今後の展望と課題
省エネと安定稼働の両立
温度や圧力の安定制御は安全性向上だけでなく、エネルギー消費の削減にも直結します。過剰に冷却・加熱・圧縮を行うことなく、必要最小限の操作で目標を達成できれば、CO₂排出量削減や電力・燃料の節約につながります。脱炭素社会を目指す現代では、各種先進制御技術が「いかに省エネ運転を実現するか」を主眼に研究されるでしょう。
現場での実装上の課題
- センサー信頼性:温度計や圧力計の故障・ドリフトに対して、冗長化や定期的な校正が必要。誤った測定値を制御に反映すると、かえって危険。
- ブラックボックス化:AIや高度制御を導入すると、オペレーターが制御の意図を理解できず、トラブル時に即応が難しい場合がある。
- 既存設備との統合:古いプラントに新しい制御システムを導入する際、既存の配線・制御ロジックと合わせるための改修が大規模になることがある。
段階的に試験導入し、効果と安全性を確認しながら拡張する実務アプローチが望ましいです。
専門家・技術者としての視点
- 物理モデルの知識:PID制御は汎用的だが、対象プロセスの熱収支・質量収支・圧力損失などを理解し、制御系のダイナミクスを把握することがゲイン調整の大前提。
- 制御理論と実践の融合:理論的に正しい制御パラメータでも、現場のノイズや設備特性の非線形性が大きいと上手く動かない場合がある。実機検証と微調整が不可欠。
- MPC・AIへのステップアップ:PID単一ループで問題が解決しない規模や複雑度になれば、MPCやAIによる多変数最適化へ移行を検討。
- 安全設計との連携:温度・圧力制御が破綻した場合を想定し、緊急冷却や圧力開放弁を配備し、暴走や爆発を回避する二重三重の安全策が必要。
まとめ
PID制御による温度や圧力の制御は、化学プラントや各種プロセス産業で最も広く使われている制御手法の一つです。
- 基礎:PID制御の簡潔な数式とループ設計により、温度・圧力を安定化し、製品品質や安全性を高める。
- 実務:反応器の温度管理や配管圧力制御で多用され、オペレーターの負担軽減や生産効率向上に寄与。
- 最新技術:自動チューニングやMPC・AIとの連携が進み、外乱やセンサー故障に強い高度制御へ発展中。
- 今後の展望:省エネルギー・脱炭素の要請が高まり、設備改修やオペレーター教育を含む総合的な制御システムのアップグレードが進む。
最終的には、適切にチューニングされたPID制御が、過度な操作や人為的ミスを減らし、安定稼働と安全性を確保する要となります。技術者は、実際のプロセス動特性と理論知識を融合し、段階的なアプローチで制御系の性能を最大限に引き出していくことが求められます。