はじめに:流量・液面制御の重要性
化学プラントや食品・医薬・石油精製など、さまざまな分野で流量と液面の安定制御は生産工程の要となります。たとえば、蒸留塔では給液量やタワー底の液面を適切に維持することで、蒸留分離の効率や製品品質を安定させます。タンクの液面制御でも、原料を一定量ずつ後工程に送ることで、ライン全体がスムーズに動作し、オペレーターの負担を軽減できるでしょう。
こうした制御において歴史的に広く用いられてきたのがPID制御(比例・積分・微分制御)です。温度や圧力などに加え、流量・液面といったプロセス変数を安定させるためのスタンダードなアプローチであり、シンプルながら高い汎用性を持つ制御手法として根強い支持があります。
基礎:PID制御とは
PID制御の基本式
PID制御は、目標値(セットポイント)と実際のプロセス値(PV)の偏差をもとに、操作量(MV)を以下の3要素で加算して求めます。
PID制御の基本式:
$$ u(t) = K_p \, e(t) \;+\; K_i \int_0^t e(\tau)\,d\tau \;+\; K_d \frac{d\,e(t)}{dt} $$
変数の定義:
\( e(t) \): 偏差(目標値 – 現在値)
\( K_p \): 比例ゲイン
\( K_i \): 積分ゲイン
\( K_d \): 微分ゲイン
このシンプルな数式が、流量や液面などの制御対象に対しても十分な性能を発揮してきました。
流量制御と液面制御の特徴
- 流量制御:ポンプの回転数やバルブ開度を操作量とし、流量計で測った値が目標流量になるようPID制御する。配管の圧損変動や下流工程の負荷変動に対応しやすい。
- 液面制御:タンクの液面を一定に維持するため、給液バルブまたは排出バルブを操作量とする。オフセット(一定偏差)の残りやすさを積分項がカバーし、長期的な液面ドリフトを除去する。
PID制御を適用する際は、偏差の時間的変動特性に基づき、ゲイン(P・I・D)を適切にチューニングする必要があります。
実務:流量・液面制御におけるPIDの導入
蒸留塔の給液量や底部の液面制御
蒸留塔では、塔頂からの戻りリフラックス量や原料給液量をPID制御する場合が多いです。さらに、タワー底の液面も制御対象となり、以下のような構成が典型例となります。
- 底部液面ループ:タンク底の液面計からの信号をPIDで受け取り、排出バルブを開閉して液面を一定に保つ。
- 給液量ループ:原料供給ポンプやバルブをPID操作し、流量計が示す目標流量に合わせる。
安定した運転が保たれると、塔内の温度や圧力といった他の制御系もスムーズに動作しやすく、製品純度のばらつきが低減します。
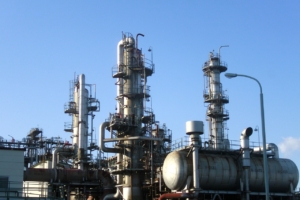
タンクの液面制御
貯蔵タンクでは、オペレーターが目で確認しつつ手動弁を調整していた時代も長かったですが、現代はほとんどが液面計 + PID制御で自動化されています。
- 投入バルブ制御型:タンクの液面が下がりすぎると給液バルブを開き、狙いの液面まで上昇すればバルブを閉じるように制御する。
- 排出バルブ制御型:タンク液面が上昇すると自動で排出を増やし、目標より下がると排出を絞る。
運転の柔軟性が高まり、オペレーターの監視作業を大幅に削減できる点がメリットです。
最新技術:高度制御とAIの導入
自動チューニングとモデル予測制御(MPC)
PID制御はシンプルながら、ゲインの設定次第で制御性能が大きく変化します。近年は以下のアプローチが実務に取り入れられています。
- 自動チューニング:ステップ応答や振動応答をAIが解析し、最適なP・I・Dを自動で提案 → オペレーターが細かいパラメータ調整に煩わされずに済む。
- モデル予測制御(MPC):単一ループだけでなく、複数の流量ループや液面ループを同時に制御し、干渉(相互影響)を考慮することで、プロセス全体の効率を高める。蒸留塔全体で見ると、リフラックス量・底部液面・加熱量など多変数を一括最適化可能。
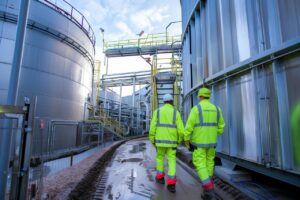
AI活用による予測と異常検知
大量の運転データやセンサー情報をAIで学習し、将来の流量・液面のトレンドを予測して事前に操作する研究が進んでいます。以下の利点が期待されます。
- 負荷変動の先読み:原料組成の変動が大きいときでも、AI予測により急激な液面変化やダイナミックな流量乱れを抑制。
- 異常検知:センサーやバルブが故障した際の異常挙動をAIが把握し、運転者に早期警告。
これにより、より小さな誤差で流量・液面を安定させるとともに、トラブル時の初動対応を迅速化することが可能です。
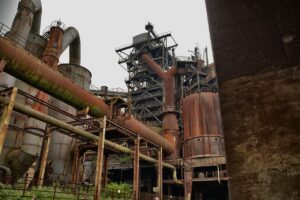
今後の展望と課題
省エネルギーと脱炭素への寄与
流量や液面制御は、プロセスの安定性だけでなく省エネルギーや環境負荷低減にも直結します。適正な給液や排液が保たれていれば、蒸留塔や反応器の運転が無駄に乱れることなく、加熱・冷却やユーティリティ使用量を最小限に抑えやすくなるでしょう。また、高効率運転はCO₂排出削減にもつながり、脱炭素社会のニーズを満たす一助となります。
現場での課題:センサー故障や大きな外乱
高度なPIDやMPCを導入しても、センサー故障や大規模負荷変動(例:原料切り替え、緊急停止など)に対する頑健性が十分でなければ、安全運転を損ねる恐れがあります。
- 冗長センサーの配置:万一1つの流量計や液面計が故障しても、他の測定値で代替できるよう設計。
- フェイルセーフ対応:制御系が破綻した場合に自動停止や緊急排出を行う仕組み。
- 定期キャリブレーション:長期運用でセンサー漂移が起き、オフセットエラーが積み上がるのを防ぐ。
さらに、オペレーター教育も欠かせず、高度制御に依存しすぎず緊急手動操作に備える体制が求められます。
専門家・技術者としての視点
- プロセスダイナミクスの理解:流量・液面は比較的ゆっくりと変化する傾向があるが、背後に隠れた負荷変動のメカニズムを把握し、適切な制御帯域を設定。
- P・I・Dゲイン調整:液面制御では大きな積分成分を用いる一方、流量制御は比例成分重視など、制御対象の動特性に合わせたチューニングが重要。
- 多変数制御への移行:単一ループPIDで済む段階から、多数のループが相互干渉する段階へと規模・複雑度が上がると、MPCやAIを含む高度制御が真価を発揮。
- 安全性確保:異常シナリオを事前に検討し、バルブ故障時のリークや液面溢流を防止する緊急措置を用意。
まとめ
「PID制御:流量・液面制御」は、化学工学やプラント運営において欠かせない基盤技術の一つです。
- 基礎として、PID制御の単純明快な数式とループ構成があり、流量計や液面計で得た偏差をリアルタイムに補正することで、目標値を安定的に維持。
- 実務では、蒸留塔の給液・排液、タンクの液面、パイプライン流量など、多岐にわたる場面で活用し、オペレーター負荷と運転コストを削減。
- 最新技術では、AIやMPCを組み合わせて最適化制御に進化し、外乱やセンサー漂移にも強いシステムを構築。
- 今後の展望として、省エネルギー・脱炭素の観点が強まり、全体プロセスの効率向上をめざす多変数制御への移行が進む一方、現場ではセンサー故障対策や人材育成が課題となる。
最終的に、適切な流量・液面制御が成されれば、上下流工程の安定と品質向上が達成され、プラント全体での生産性が飛躍的に高まります。PIDのような一見古典的な制御も、AIやデジタル技術と融合することで新たな可能性を切り拓いており、今後も研究・応用が盛んに続けられるでしょう。