PID制御(Proportional-Integral-Derivative Control)は、対象となるプロセスの制御量(温度、圧力、流量など)を目標値に保つために用いられる、最も基本的かつ広く普及している制御手法です。その名が示すとおり、以下の3つの要素から構成されます。
P(比例): 制御偏差(目標値と現在値の差)に比例した操作量を出力。
I(積分): 過去からの偏差を累積的に評価し、オフセット(偏差が一定値残る現象)を除去。
D(微分): 偏差の変化率を評価し、急激な変動に対して先行的に制御信号を加える。
PID制御は、数学的に比較的シンプルかつ汎用性が高いため、プロセス産業はもちろん、自動車やロボット制御などさまざまな分野で用いられています。化学工学の現場では、蒸留塔の温度制御、タンクの液面制御、反応器の温度や圧力調整など、多彩なプロセスに適用されており、設備の安定稼働と製品品質の向上に大きく寄与します。
PID制御の基本式:
$$ u(t) = K_p e(t) + K_i \int_0^t e(\tau)\,d\tau + K_d \frac{de(t)}{dt} $$
変数の定義:
\( u(t) \):操作量(制御信号)
\( e(t) \):偏差(目標値と現在値の差)
\( K_p \):比例ゲイン(P成分の強さ)
\( K_i \):積分ゲイン(I成分の強さ)
\( K_d \):微分ゲイン(D成分の強さ)
P(比例)制御:
$$ u_P(t) = K_p e(t) $$
比例項は、現在の偏差に比例して操作量を出力します。大きな偏差には大きな制御出力で応答し、すばやく目標値に近づけるように働きます。
I(積分)制御:
$$ u_I(t) = K_i \int_0^t e(\tau)\,d\tau $$
積分項は、過去からの偏差を蓄積して操作量に反映させます。一定の偏差(オフセット)が残る場合にも、それを徐々に解消してゼロ偏差に導きます。
D(微分)制御:
$$ u_D(t) = K_d \frac{de(t)}{dt} $$
微分項は、偏差の変化速度に基づいて操作量を調整します。急激な変動に対して先読み的に制御信号を与え、応答性を高める効果があります。
実務での使いどころ
温度や圧力の制御
化学プラントでは、温度管理が生産効率と安全性を左右するケースが非常に多いです。たとえば、反応器の内部温度が高すぎると副反応が増えたり、暴走反応を引き起こすリスクがあります。逆に低すぎると生産性が落ちることもあるので、PID制御によって適切な加熱・冷却バランスを保つのが一般的です。圧力容器やパイプラインの圧力制御にも同様にPIDが使われ、安定したプロセス運転を可能にしています。
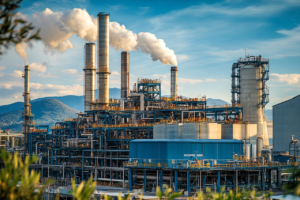
流量・液面制御
蒸留塔やタンクの液面制御には、入力流量と出力流量をPIDで調整する方法がよく採用されます。タンク内部の液面が上昇しすぎないよう、排出バルブを開いたり、逆に液面が低下したら給液バルブを操作したりと、リアルタイムで自動調整を行うことで、オペレーターの手間を削減しながら安定稼働を確保できます。流量制御においても、ポンプの回転数やバルブ開度をPIDで制御することで、目標流量を保ちつつプロセス全体の効率を高めることが可能です。
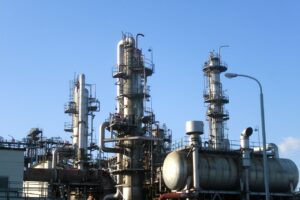
装置の立ち上げ・停止時の安全確保
化学工場などの大規模プラントでは、装置の立ち上げやシャットダウンの際にパラメータが大きく変化しやすく、制御が乱れがちです。PID制御を適切に調整しておくことで、温度や圧力の急変を抑え、安全に稼働状況を移行できます。特に反応器など、反応速度と温度の相互作用が強いプロセスでは、PIDの設定が甘いと短時間で暴走的な温度変化が発生し、大事故につながるリスクがあります。
最新技術
モデル予測制御(MPC)との組み合わせ
PID制御はシンプルで堅牢ですが、プロセスが多変数かつ相互干渉が大きい場合、伝統的なPIDだけでは十分に制御性能を出せない場面があります。そこで近年注目されているのが、モデル予測制御(MPC) などの高度制御手法です。MPCはプロセスの数理モデルを用いて先を見越した操作を行い、複数の制御量と操作量を同時に最適化します。PID制御とのハイブリッド構成を採用し、大枠の動的制御をMPCが担当し、微調整をPIDで行う事例も増えています。
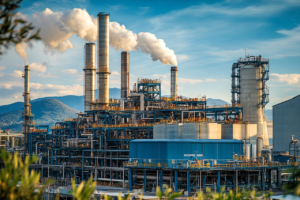
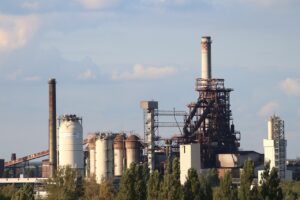
AIや機械学習を活用したパラメータ自動調整
PID制御には、ゲイン(Pゲイン、Iゲイン、Dゲイン)の適切な調整が不可欠です。しかし、実際のプラントでは装置特性や外乱(周囲環境や原料特性など)が頻繁に変化するため、ゲインを固定しておくと十分な制御性能が得られない場合があります。近年は、AIや機械学習を使ってリアルタイムにゲインを調整し、自己チューニングするアプローチが注目されています。クラウドや工場内サーバーでデータを蓄積し、プロセス動作の傾向から最適ゲインをフィードバックする技術が、一部で実用化され始めています。
デジタルツインと遠隔制御
IoT技術の普及に伴い、プラントのデータをリアルタイムで取得し、仮想空間上に装置やプロセスの“デジタルツイン”を構築する事例が増えています。デジタルツイン上でPID制御や高度制御のシミュレーションを行い、最適な操作方針を導き出して現場に反映するという流れが徐々に定着してきました。また、遠隔地からの操作や、異常時に自動アラートを発する仕組みを組み合わせることで、少人数・少コストでの安定運転を実現するプラント運営が加速しています。
今後の展望
複雑プロセスへの適用拡大 反応と分離、触媒プロセスや膜分離など、多段階・高次元のプラントでは、従来のPID制御がしばしば限界に近いと考えられています。しかし、必要に応じてMPCやAIを部分的に導入しながら、各局所の単ループ制御はPIDで安定化を図るというハイブリッド戦略が今後も主流となるでしょう。特に温度、圧力、流量などの主要パラメータにおいては、慣性が大きく変化が緩やかなため、PIDのシンプルさは依然として強い武器です。
セルフチューニング技術の進化 企業や研究機関は、セルフチューニングPIDの精度向上を模索し続けています。機械学習だけでなく、メタヒューリスティックス(遺伝的アルゴリズムや粒子群最適化など)を活用したパラメータ探索が進めば、プロセスに合わせてより迅速かつ最適なゲイン調整が可能になるでしょう。この技術がさらに成熟すると、制御エンジニアが一からゲインを試行錯誤する手間が大幅に削減され、運用コストやトラブルリスクを下げられます。
サイバーセキュリティとの連携 プラントの制御システムがネットワークでつながるほど、サイバー攻撃のリスクも高まります。PID制御ループ自体にはあまり複雑なセキュリティが求められないように思われがちですが、近未来のスマートプラントでは遠隔制御やクラウド上でのデータ解析など、あらゆる通信が標準となる見込みです。そのため、PID制御や制御ネットワークの異常検知システムを組み込み、攻撃や誤作動を早期に察知してシステムを安全な状態に戻す仕組みづくりが欠かせなくなるでしょう。
まとめ
PID制御(PID Control)は、比例・積分・微分の3要素で制御偏差を調整し、プロセスを所望の状態に保つという、制御工学の基礎を形作る手法です。化学プラントの温度制御や液面制御など、多岐にわたる分野で長年にわたり利用され、その信頼性と分かりやすさは今も揺るぎないものがあります。
しかし、プラントの大型化・複雑化、環境変化や競合環境の激化に伴い、より高精度かつ柔軟な制御が求められています。そこで、モデル予測制御との連携やAIを活用した自動チューニング、デジタルツインを使ったリアルタイム最適化などが今後の主流となり、PID制御はそれら高度制御を支える土台として進化を続けるでしょう。最適化と安全運転の両立という観点からも、PID制御は引き続き欠かせない存在であり、制御エンジニアにとって永遠の学びのテーマと言えます。