はじめに:熱交換器の役割と重要性
化学プラントでは、反応器や蒸留塔と並んで“熱交換器”は不可欠な機器です。たとえば原油を常圧蒸留塔に送る前に加熱するヒータ、蒸留塔頂からの留分を凝縮するコンデンサー、あるいは化学反応後の生成物の温度を下げるクーラーなど、多様な熱交換器が稼働しています。適切に設計され、最適に運転されれば、エネルギー効率の向上や生産性アップ、運転コストの低減につながります。しかし、いったん設計や運用を誤れば、熱交換効率の低下や装置の汚れ(ファウリング)問題が生じ、プラント全体の性能を損ねるリスクがあります。
基礎:熱交換器の原理と伝熱係数
伝熱の三形態と熱交換の基本
伝熱(Heat Transfer)は大きく伝導、対流、放射の3つに分類され、熱交換器では主に前2つ(伝導と対流)が組み合わさって熱移動が起こります。パイプやプレート壁を介して高温流体から低温流体へ熱が移る過程は、理想的には以下の式に集約されます。
熱交換量の式:
$$ Q = U \, A \, \Delta T_{\text{lm}} $$
変数の定義:
\( Q \): 熱交換量
\( U \): 総括伝熱係数
\( A \): 伝熱面積
\(\Delta T_{\text{lm}}\): 対数平均温度差
この式からわかるように、熱交換器の設計や運転を考えるうえで、総括伝熱係数𝑈、伝熱面積𝐴、そして流体間の温度差
Δ𝑇lmが主要なパラメータとなります。

総括伝熱係数𝑈と流体力学
総合伝熱係数𝑈 は、流体側の対流伝熱係数、壁面の伝導抵抗、汚れ(ファウリング)抵抗などをすべて含んだ係数です。化学プラントでは、しばしば以下のような要因が伝熱係数を複雑にします。
- 流体の粘度・熱伝導率・乱流度合い
- 流速が変わると、境膜伝熱係数が非線形に変化する
- スケーリングやコーキングと呼ばれるファウリング層の付着により、時間経過とともに係数が低下
これらを正確に把握・推定することが、熱交換器設計・運転の基礎となります。設計段階で使用する図表(Nu数やRe数の相関式)や、CFD(数値流体力学)解析を活用することで、より精緻に𝑈を見積もることが可能です。
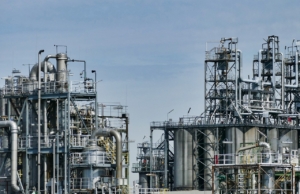
実務:熱交換器の最適設計・運転
型式選択とレイアウト
一口に「熱交換器」といっても、シェル&チューブ式、プレート式、螺旋式、エアクーラー式など多彩な型式があります。それぞれに特徴があり、流体特性(粘度・腐食性・粒子含有など)や運転条件(圧力、温度差、許容圧損)によって選定が異なります。
- シェル&チューブ式:汎用性が高く、広範囲な圧力温度に対応可能
- プレート式:伝熱面積をコンパクトに確保でき、掃除がしやすい
- 螺旋式:高粘度流体やファウリング傾向が強い用途に有効
- エアクーラー式:冷却水が手に入りにくい場所や高温ガスの冷却に最適
実務では、装置全体のPFD(Process Flow Diagram)や運転コスト、掃除のしやすさなど総合的に考えてレイアウトを決定します。
流体流速・圧力損失のバランス
熱交換器での伝熱は、流体流速を高めるほど境膜伝熱係数が大きくなり効率は向上しますが、その分圧力損失やポンプ動力が増大し、運転コストがかさみます。また、過度に高速な流れは振動やエロージョンによる管の損傷、騒音を招くことがあります。
したがって、熱交換器のチューブ内流速は通常 1〜2 m/s 程度が目安とされますが、流体の性質や汚れ易さに応じて微調整されます。これは実務での最適化の主要テーマであり、エネルギーバランスやメンテナンス負担とも関係します。
ファウリング対策と清掃
運転を続けると、固形物の沈着や化学反応生成物の付着によって伝熱面が汚れ(ファウリング)伝熱性能が低下します。結果として、設計時の期待伝熱係数が得られず、チューブ側圧損が増大して流量が確保できなくなるなどの問題が起こります。
ファウリング対策としては、以下が一般的です。
- 定期清掃スケジュール(CIP、機械的ブラシ洗浄など)
- 水質管理・添加薬品(腐食防止剤、スケール防止剤)
- 流速管理:適度に乱流を維持し、スケールや沈殿を付きにくくする
- 表面材質選定(耐腐食性、容易洗浄)
ファウリングを早期に検知するため、チューブ側とシェル側の温度・圧力差の変動を常時監視して、異常時に洗浄を行う運用も重要です。
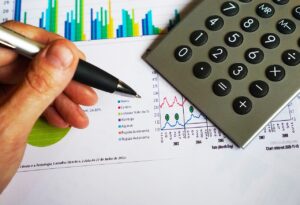
最新技術:CFD解析とAIの応用
CFDによる詳細解析
従来、熱交換器の設計は 経験相関式や標準的な伝熱モデル で行われてきましたが、近年はCFD(数値流体力学)解析が実務で普及しつつあります。
- 流体の速度分布・乱流強度、温度分布を三次元的にシミュレート
- 局所的なホットスポットやデッドゾーンを発見し、設計修正
- チューブ束内部の流れ不均一や逆流等の問題を可視化
特に複雑形状のプレート式熱交換器や、エロージョン・腐食が懸念される領域ではCFDによる検討が大きな効果を持ちます。
AI・機械学習でのリアルタイム診断
運転段階では、IoTセンサーによって取得した流量・温度・圧損データなどをAIがオンライン解析し、伝熱性能の低下やファウリングの進行を早期に検出する事例が増えています。
- 異常検知モデル:健全運転時のデータを学習し、ファウリングが発生すると伝熱係数や圧力損失が急変 → アラート発信
- 予測メンテナンス:AIが洗浄タイミングを予測し、定期停止を最小限に抑える
- 最適制御との連携:蒸留塔や反応器と連携して、余剰熱の再利用や冷却負荷を最適化
これにより、プラント全体での省エネルギーを追求しながら、装置の寿命を延ばす運用が期待されています。

今後の展望:省エネと持続可能性への貢献
プロセス統合と熱ネットワーク
単体の熱交換器の最適設計だけでなく、近年はプロセス全体の熱統合(Heat Integration) が注目されています。Pinch技術やエクセルギー解析を組み合わせて、廃熱を別工程に再利用するなど、プラント全体でエネルギー効率を高める取り組みが進みます。
- 高温排ガスを別の反応器や加熱工程の熱源に利用
- CO₂削減を目指した熱ポンプ蒸留や吸着式冷凍機の併用
熱交換器の配置や運転条件を統合的に最適化することで、省エネ率が数%以上改善し、CO₂排出量を削減できるケースも多いです。
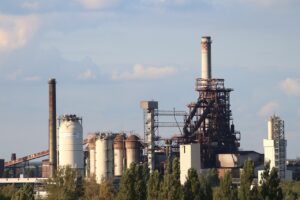
先端材料と持続可能設計
材料面では、高熱伝導かつ耐腐食性に優れた合金や樹脂材料、さらには表面コーティングによる汚れ付着防止といった開発が進んでいます。
- 耐摩耗合金、セラミックコーティング
- 親水/疎水表面制御でスケールを剥がれやすくする
また、持続可能性の観点から再生可能エネルギーと連携する熱交換ネットワークや、排熱回収システムの開発も進んでおり、これらが実装されれば化学工業の環境負荷が大きく低減することが期待されます。
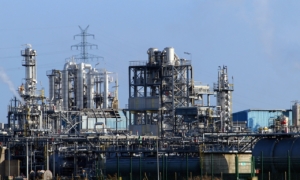
専門家・技術者としての視点
- 高度解析ツールの活用:CFDやAI技術を使う場合、ブラックボックス化を防ぎ、物理的な意味付け(境膜係数や圧力損失の整合性)を常に確認する。
- 現場データのフィードバック:設計段階の相関式だけでなく、稼働中の温度・圧損・ファウリング速度を継続的に記録し、改良サイクルを回すことが重要。
- メンテナンス計画との統合:ハイパフォーマンスな設計も、清掃・点検が追いつかなければ性能低下を招く。運転条件とメンテナンススケジュールを連携する仕組みが鍵。
特に化学工場の生産技術や設備管理に携わるエンジニアは、総合伝熱理論の理解と、実測データを活用する実務感覚の両方が求められます。材料や腐食防止技術も含めたマルチディシプリンな視点が必要でしょう。
まとめ
熱交換器の設計・運転は、化学プラントのエネルギー効率・生産効率を左右する重要テーマです。最適な伝熱係数の推定、流体流速・温度分布の解析を行い、適切な熱交換面積や設計を確保することで、設備の信頼性と運転コスト削減を両立できます。
- 基礎:伝熱の三形態と総括伝熱係数𝑈 の理解が不可欠。汚れ(ファウリング)や流体特性を考慮した正確なモデリングが重要。
- 実務:シェル&チューブ式やプレート式など、多種多様な熱交換器の型式を使い分け、最適な流速や清掃戦略で運用。ファウリング検知やCIP計画が欠かせない。
- 最新技術:CFD解析やAIを用いた異常検知・予測メンテナンスが普及しつつあり、デジタルツイン化による運転最適化が進む。
- 今後の展望:省エネ・CO₂排出削減の要求が高まり、プロセス全体の熱統合や高性能材料の採用が加速。化学工学エンジニアは計算ツールと現場データの融合で、より高度な設備管理を実現する。
最終的に、熱交換器の運用が成功するかどうかは、“正確な設計+継続的な運転データのフィードバック+計画的メンテナンス”の総合力で決まります。常に現場の変化を捉え、設備をアップデートしていく姿勢こそが、現代の化学プラントに求められるアプローチといえるでしょう。